Cilindro e Rosca para Extrusora: Tudo Que Você Precisa Saber
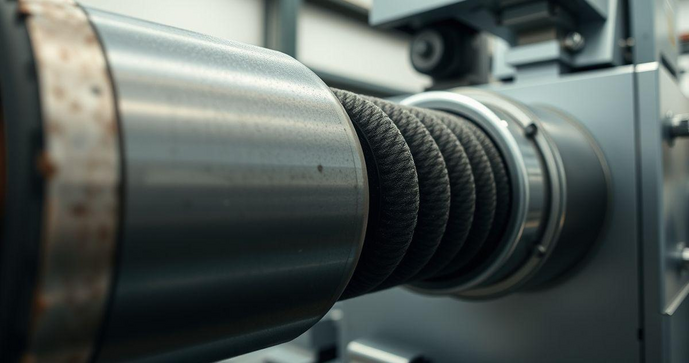
Por: Marcos - 17 de Abril de 2025
Função do Cilindro na Extrusão
O cilindro desempenha um papel fundamental no processo de extrusão, sendo responsável por aquecer e empurrar as matérias-primas através da rosca. Sua construção e design são elaborados para garantir que o material seja processado de maneira homogênea e eficiente.
Durante a extrusão, o cilindro fornece o calor necessário para derreter plásticos ou outros materiais, facilitando sua transformação em um estado fluido. Isso ocorre devido à combinação de temperatura controlada e à pressão exercida pela rosca em movimento, que avança o material na câmara de extrusão.
A eficiência do cilindro é crucial, pois pode afetar diretamente a viscosidade do material processado, impactando características como a resistência e a fluidez no produto final. Um cilindro projetado com tecnologia avançada proporciona melhor controle térmico, que é essencial para reduzir variações que podem prejudicar a qualidade do extrudado.
Além disso, o cilindro também atua como um reservatório temporário para o material. À medida que o material é alimentado, ele é armazenado no cilindro antes de ser forçado através da rosca, permitindo um fluxo constante e controlado. Esse armazenamento temporário é crucial em processos de produção contínua, onde consistência e qualidade são primordiais.
Em resumo, o cilindro não apenas aquece e empurra o material, mas também desempenha um papel vital na manutenção da qualidade do produto, garantindo que as propriedades do material sejam respeitadas e potencializadas durante todo o processo de extrusão.
Tipos de Roscas para Extrusoras
As roscas para extrusoras são componentes essenciais que influenciam diretamente a eficiência do processo de extrusão e a qualidade do produto final.
Existem diversos tipos de roscas, cada uma projetada para atender necessidades específicas de processamento.
Abaixo, destacamos os principais tipos de roscas utilizados na indústria.
1. Rosca Simples: Esta é a forma mais comum de rosca, composta por um único canal.
É geralmente utilizada para materiais que não exigem processamento complexo e proporciona uma taxa de extrusão eficiente.
É ideal para aplicações gerais, como a extrusão de plásticos comuns.
2. Rosca Dupla: Consiste em dois canais que permitem um maior fluxo de material, aumentando a capacidade de extrusão.
Este tipo de rosca é indicado para materiais com alta viscosidade ou que requerem mistura intensa, uma vez que promove um movimento mais homogêneo do material.
É frequentemente utilizada em aplicações de engenharia de polímeros.
3. Rosca de Ação Dupla: Similar à rosca dupla, mas projetada com geometrias específicas que melhoram a distribuição de temperatura e a mistura do material.
É ideal para compostos que exigem adição de corantes ou aditivos durante o processo de extrusão.
4. Rosca Consoante: Este tipo apresenta um formato que permite uma melhor compressão do material, ideal para produtos que exigem alta densidade.
A geometria da rosca consoante pode ser ajustada para otimizar a pressão e a temperatura, aumentando a eficiência no processamento de materiais difíceis.
5. Rosca de Turbo: Uma rosca avançada que utiliza múltiplas seções de transmissão para criar um efeito de mistura mais intensivo.
Essa configuração é adequada para materiais que precisam de uma homogeneização rápida e efetiva, como compostos alimentícios ou plásticos com adição de fibras.
Em conclusão, a escolha do tipo de rosca dependerá das especificidades do material a ser processado e da aplicação final do produto.
A correta seleção da rosca é essencial para maximizar a eficiência do processo de extrusão e garantir um produto de alta qualidade.
Materiais Utilizados na Fabricação
A escolha dos materiais utilizados na fabricação de cilindros e roscas para extrusoras é crucial para garantir o desempenho, a durabilidade e a eficiência do equipamento. Diferentes aplicações e tipos de materiais exigem materiais específicos que atendam às exigências operacionais.
1. Aço Carbono: Um dos materiais mais utilizados na fabricação de cilindros e roscas. O aço carbono é valorizado por sua resistência, durabilidade e facilidade de usinagem. Este material é frequentemente aplicado em extrusoras que processam plásticos comuns, pois oferece uma boa relação custo-benefício e suporta altas temperaturas e pressões.
2. Aço Inoxidável: Este material é ideal para aplicações que envolvem processos alimentícios, químicos ou farmacêuticos, onde a contaminação deve ser evitada. O aço inoxidável possui alta resistência à corrosão, facilitando a limpeza e mantendo a integridade do material processado. Sua durabilidade também é um fator importante em ambientes de produção exigentes.
3. Materiais Revestidos: Em algumas aplicações, cilindros e roscas são revestidos com materiais especiais, como teflon ou cerâmicas, para melhorar a resistência ao desgaste e reduzir a fricção. Esses revestimentos ajudam a prolongar a vida útil do equipamento e a melhorar o desempenho no processamento de materiais abrasivos ou sensíveis ao calor.
4. Composites de Alumínio: Utilizados em aplicações específicas onde a leveza e a resistência à corrosão são essenciais. Os compósitos oferecem uma alternativa interessante ao aço, com uma excelente relação entre peso e resistência. Apesar de não serem tão comuns, representam opções inovadoras para a fabricação de componentes de extrusoras.
5. Bronze e Messing: Esses materiais são frequentemente utilizados para componentes que exigem resistência ao desgaste e boa condutividade térmica. Bronze e messing são também preferidos em aplicações onde a corrosão pode ser um problema, proporcionando uma durabilidade superior em ambientes adversos.
Em resumo, a seleção dos materiais utilizados na fabricação de cilindros e roscas para extrusoras deve ser feita com base nas necessidades específicas do processo de extrusão, levando em consideração fatores como temperatura, pressão, e as propriedades dos materiais a serem processados. Optar por materiais adequados é vital para garantir um desempenho eficiente e prolongar a vida útil do equipamento.
Dimensionamento e Projetos Personalizados
O dimensionamento e a elaboração de projetos personalizados para cilindros e roscas de extrusoras são etapas fundamentais para otimizar o desempenho e a eficiência de processos de extrusão. Essas práticas garantem que o equipamento atenda a requisitos específicos, como tipos de materiais, capacidades de produção e características desejadas no produto final.
1. Análise de Requisitos: O primeiro passo no dimensionamento é entender as necessidades do processo. Isso inclui considerar o tipo de material a ser processado, a taxa de extrusão desejada e as propriedades mecânicas do produto final. A análise deve levar em conta fatores como a viscosidade do material, temperatura de processamento e condições operacionais.
2. Geometria da Rosca: O design da rosca é crucial e deve ser ajustado com base nas características do material. Para materiais com alta viscosidade, pode ser necessário projetar uma rosca com um ângulo e uma profundidade de canal específicos para facilitar o fluxo e a mistura. O comprimento da rosca e a configuração do canal podem impactar diretamente a eficiência do processo.
3. Capacidade de Carga: O dimensionamento também deve considerar a capacidade de carga do cilindro e da rosca. Isso envolve calcular a pressão máxima que o sistema pode operar sem comprometer a integridade estrutural dos componentes. Um projeto bem elaborado assegura que o cilindro e a rosca suportem a pressão durante todo o ciclo de produção, evitando falhas ou desgastes prematuros.
4. Materiais e Acabamentos: A escolha dos materiais utilizados na fabricação deve alinhar-se ao dimensionamento e ao projeto. É vital considerar não apenas as propriedades mecânicas, mas também os requisitos de resistência à corrosão e ao desgaste, dependendo do tipo de material a ser processado. Acabamentos especiais podem ser projetados para aumentar a eficiência do processamento.
5. Personalização e Prototipagem: Uma abordagem personalizada permite a adaptação de cilindros e roscas a necessidades específicas. Utilizando técnicas de prototipagem e simulações, as empresas podem testar e validar os projetos antes da produção final. Isso minimiza erros e assegura que os produtos atendam às expectativas de desempenho.
Em suma, o dimensionamento e os projetos personalizados de cilindros e roscas para extrusoras são essenciais para maximizar a eficiência e a qualidade do processo de extrusão. Um projeto bem elaborado, baseado nas características e nas exigências dos materiais, garante a durabilidade e a funcionalidade do equipamento, resultando em um produto final superior.
Manutenção e Dicas para Otimização
A manutenção adequada dos cilindros e roscas para extrusoras é essencial para garantir um desempenho contínuo e eficiente no processamento. Além de evitar custos elevados com reparos, a manutenção regular também contribui para a qualidade do produto final.
A seguir, estão algumas práticas recomendadas e dicas para otimizar a vida útil desses componentes.
1. Inspeções Regulares: É fundamental realizar inspeções periódicas para identificar sinais de desgaste ou falhas. Verifique se há rachaduras, corrosão ou deformações na superfície do cilindro e da rosca. Inspeções visuais podem ajudar a detectar problemas antes que se agravem, garantindo a continuidade da operação.
2. Limpeza Frequente: A limpeza deve ser uma parte integral da manutenção. Resíduos de material podem se acumular, impactando a eficiência do equipamento. Utilize produtos adequados para a limpeza, evitando químicos que possam danificar o material do cilindro ou da rosca. Uma boa prática é realizar a limpeza após cada ciclo de produção ou sempre que trocas de materiais forem feitas.
3. Lubrificação: A lubrificação correta das partes móveis é crucial para evitar o desgaste prematuro. Siga as recomendações do fabricante quanto à frequência de lubrificação e utilize óleos ou graxas compatíveis. O excesso ou a falta de lubrificante pode causar problemas, portanto, mantenha um balanço adequado.
4. Ajustes e Calibrações: Com o tempo, pode ser necessário realizar ajuste nas configurações do cilindro e da rosca. Verifique frequentemente as configurações de temperatura e pressão, ajustando-as conforme a necessidade do processo. Uma calibração correta assegura um desempenho otimizado e uma melhor homogeneização do material.
5. Monitoramento de Desempenho: Incorporar ferramentas de monitoramento pode ajudar a acompanhar o desempenho do cilindro e da rosca. Sensores e sistemas de automação permitem a detecção antecipada de falhas, reduzindo o tempo de inatividade e aumentando a eficiência produtiva. Analisando dados em tempo real, fica mais fácil tomar decisões de manutenção mais informadas.
6. Substituição de Componentes: Identificar quando é necessário substituir partes desgastadas é vital para manter a eficiência do sistema. Componentes como rolamentos, selos e aquecedores podem ter uma vida útil limitada e precisam ser trocados regularmente para evitar problemas maiores.
7. Registros de Manutenção: Manter um histórico detalhado das práticas de manutenção é essencial para identificar padrões ou problemas recorrentes. Isso ajuda a prever necessidades futuras de manutenção e a tomar decisões fundamentadas sobre melhorias no processo.
Em resumo, a manutenção regular e as dicas de otimização para cilindros e roscas para extrusoras são essenciais para garantir o funcionamento eficiente e a longevidade dos equipamentos. Ao seguir essas orientações, é possível maximizar a produção e manter a qualidade dos produtos finais.
Impacto na Qualidade do Produto Final
O impacto da escolha adequada de cilindros e roscas na qualidade do produto final é um fator crítico em processos de extrusão. Compreender como esses componentes afetam as características do material extrudado ajuda a otimizar a produção e a garantir que as especificações do produtos sejam atendidas.
1. Homogeneização do Material: Um cilindro e rosca bem projetados garantem uma mistura uniforme e eficiente do material. Quando a homogeneização não é alcançada, podem ocorrer variações na densidade e na resistência do produto final. Isso é especialmente importante ao processar materiais compósitos ou plásticos que incluem aditivos ou corantes, exigindo uma distribuição uniforme para evitar falhas.
2. Controle de Temperatura: O cilindro atua como um controlador de temperatura durante o processo de extrusão. Se a temperatura não for adequadamente regulada, isso pode resultar em degradação do material, diminuição das propriedades mecânicas e alteração na aparência do produto final. Sistemas de aquecimento bem projetados dentro do cilindro garantem que o material atinja a temperatura ideal sem superaquecimento, preservando suas características.
3. Textura e Acabamento: A configuração da rosca pode influenciar a textura e o acabamento do produto extrudado. Roscagens diferentes podem resultar em diferentes forças de cisalhamento aplicadas ao material, afetando a textura superficial e a aparência estética. Produtos extrudados com diferenças de textura podem não atender às expectativas do mercado, prejudicando a aceitação do consumidor.
4. Consistência na Produção: O impacto da qualidade dos cilindros e roscas também se reflete na consistência da produção. Com um design adequado, o equipamento é capaz de operar de maneira eficiente e estável, resultando em lotes de produtos que mantêm as mesmas especificações e características. Essa consistência é vital para manter a confiança do cliente e a reputação da marca.
5. Redução de Defeitos: Componentes de alta qualidade e bem projetados ajudam a minimizar defeitos, como bolhas de ar, desintegração ou variações dimensionais, que podem ocorrer durante a extrusão. A presença de defeitos não só compromete a estética, mas também pode afetar a funcionalidade do produto final. Um sistema de extrusão eficaz contribui para a redução dessas falhas, assegurando um produto de qualidade superior.
6. Impacto na Sustentabilidade: Produtos extrudados de alta qualidade costumam ter uma melhor indexação de sustentabilidade e eficiência no uso de recursos. Um processo de extrusão otimizado reduz desperdícios e reutiliza materiais de maneira eficaz, contribuindo para práticas ambientais responsáveis e reduzindo o impacto sobre os recursos naturais.
Em conclusão, a qualidade do cilindro e da rosca exerce um impacto significativo na qualidade do produto final em processos de extrusão. A atenção a esses detalhes resulta não só na satisfação do cliente, mas também na valorização da marca e no aumento da competitividade no mercado.
Em suma, a compreensão e atenção aos aspectos relacionados ao cilindro e à rosca para extrusoras são essenciais para otimizar o processo de extrusão e garantir a qualidade do produto final.
Desde a escolha dos materiais até o dimensionamento e a manutenção, cada detalhe influencia diretamente a eficiência da produção e as características do material processado.
Ao implementar práticas recomendadas de manutenção e ao considerar a personalização de cilindros e roscas, as indústrias podem maximizar a produtividade e minimizar falhas.
Além disso, a qualidade desses componentes é crucial para atender às expectativas do mercado e promover a sustentabilidade, garantindo produtos que não apenas sejam eficazes, mas também respeitem as normas ambientais.
Portanto, investir em cilindros e roscas de alta qualidade e em um processo de extrusão otimizado não é apenas uma questão de eficiência operacional, mas também uma estratégia para garantir a satisfação do cliente e a competitividade no setor.
A excelência nessas áreas se traduz em produtos superiores e na construção de uma marca forte e confiável no mercado.